Part of my job with Tape Op is talking with our advertisers, and I particularly enjoy talking with the smaller, boutique audio makers. Of that group, Avedis Kifedjian is one of my favorite people to chat with. I have to be careful with Avedis, as our conversations can stretch into an hour before I know what happened to the time, and my head ends up bursting with new knowledge. Avedis is a smart guy, with equal measures of knowledge and experience that not too many people can match. I figured it was time to chat with him on the record, so we met up at his shop in his dad's garage in Tujunga, California.
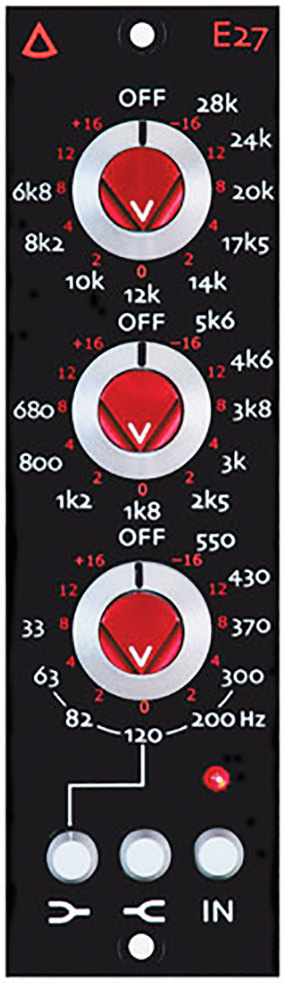
So how did you get started doing this?
It started with cars. When I was 13 years old I was fascinated with cars and how they worked with the mechanical and electrical systems. I bought my first car when I was 14 for $250 and would constantly to take things apart, clean it, and put it back together. There was still music on the radio and that was when MTV played nothing but music videos. It was music and muscle cars every day throughout my teenage years. My brother and I would listen to all kinds of records, which were often just given to us from someone who didn't want them. I was always fascinated with the sound. I'd listen to records and say, "That sounds cool. How'd they do it?" I was playing the guitar by ear and didn't know the chords I was making. I wanted to record myself, but I didn't know anybody who had a studio. When I was 18 years old, I saved up and got a Tascam 4-track cassette recorder. I didn't have any good mics, but I realized that I could just use my headphones backwards. I would plug the headphones into the mic input, place it on the guitar body, and record. Then I'd plug it back and listen; it sounded a little boomy, but it worked. I was going to college with no real direction as to what to do, and I was working full-time at a job I didn't enjoy. By 1995, I thought I'd follow what I really loved with music and recording so I went to school at the Recording Workshop in Ohio, and after months back home, I got a letter in the mail for an opening to work as an intern at Grandmaster Recorders in Hollywood. That was when I first saw a Neve console and met Geoff Tanner [Neve expert at Aurora Audio]. Working there as an intern was great, and I learned a lot because it was an old, well-used studio and a lot of equipment needed fixing. If you really want to learn as an intern, it's best to work in a studio that's not so perfect. I was in heaven because I could take these things apart and try to learn them. I'd work on microphones, headphones, power amps, guitar amps, and the Neve 8028 console with Geoff. He would hand me a schematic and a bad amp board and say, "Here, fix this." Or he would draw up a schematic with the power supply, hand it to me, and I'd have to build it. I had a skateboard at the studio because it was easier to get around in Hollywood, so I'd skate down to Yale Electronics [on Sunset Blvd.] and pick up components. David Langford worked at Yale; he was Geoff's boss from back in their Neve days and I'd ask him questions about my Neve projects. It was funny, as these two really smart guys would try to correct each other's Neve knowledge with their sense of humor. When I worked at Grandmaster, I wasn't really into being an assistant engineer, so I found ways to keep busy in the tech shop. The studio manager, Jeorgia Anderson, who had originally hired me as an intern, brought Wade in to take my place as an assistant and they put me to work with Geoff full-time. We'd work on various projects and would service Neve consoles in L.A. We even traveled to the Middle East to modify a Shep console. Looking back, I was fortunate to be there, and I knew it; but I had to get a consistent paying job, so I worked at Guitar Center. That only lasted a month or so. That's when Wade [Goeke of Chandler Limited, then working at Brent Averill] saw me there and said, "What are you doing here? Come work at Brent's!" I knew him from when he was working at a studio up the street from Grandmaster, and he told me he was working at Brent Averill's [which Brent eventually sold; it morphed into BAE Audio].
So, both you and Wade were working together at Brent's?
We did, but only for the first week or so. When I met Brent for the first time in 1999, he hired me on the spot when he found out that I knew how to build the difficult three-deck Neve gain switch. Brent's place was really organized. If you needed a part, he had everything labeled and it made things more efficient. I learned to work on API modules. I wanted to make my own op-amp, because Brent was running out of 2520s, and I didn't want to buy old 2520s. After months of working on it, I made a discrete op-amp; Brent liked it and I got to update the 312A mic pre with some improvements. Then I designed a 500 Series EQ that eventually became the E27. It was actually the first 500 Series EQ that had a transformer-balanced input and output. Older API 550As were unbalanced on their inputs and the other modules, like the 554, 560, 550A1 had electronically-balanced inputs. At the time, the 500 Series was not popular. There was only API, Brent Averill, and me with the new EQ who were making 500 Series modules.
To backtrack a little bit, at any point did you go to school or anything? Or are you totally self-taught?
I'm self-taught. The only electronics class I had was in the eighth grade. We used to make buzzers and little motors and have practical jokes in class.
Did you at any point decide that you needed to learn theory and start to dig into electronics texts?
Oh, yeah. I have a lot of books on the subject. You still gotta learn the engineering and try to understand it. I did go to college, and I took math to figure some things out. It's not just by experience – it's textbooks as well.
So, the only school you did was the math to self-study the electronics?
Yeah. There are many applications to things, like Ohm's Law, and knowing math certainly helps because you need to manipulate formulas to make the circuit work. There's only so much guesswork you can do if you don't work out the numbers. I'd study various schematics and think of how it works. I would take notes and eventually build an experiment to try new ideas. There was a lot of failure, but I'm stubborn so I just kept trying. I've come back to projects and prototypes I started years ago.
So, you basically self-educated yourself, as opposed to tinkering and figuring out things without really learning the theory behind it?
Right; I try to learn the theory while I'm tinkering. The good thing about tinkering is that if you get stuck on a problem, you can hit the textbooks and learn about that particular subject. Get stuck on enough problems and there's a lot of potential to learn. Linear power supplies are a great way to start. It's a great way to learn about components such as transformers, diodes, caps, regulators and how they work together. It's not always as difficult as it seems when you break it down. I don't love electronics. I love music. I just do electronics to get music to sound the way I like. I never thought of myself as an electrical engineer or anything like that.
You seem like one of the smarter guys in the industry about electrical engineering. Do you still play music?
Yeah, I play guitar just about every day, and now especially, with my baby. It seems to catch his attention. I can see he loves music, too.
So, the first product was the op-amp, right?
Yes, the first product was the op-amp that I originally made to fix older API modules. The 1122 op-amp also helped me come up with ways to use it in my own designs.
Tell me about your op-amp and the design of your op-amp. It's not just a copy of a 2520, right?
No, but I had to learn how the 2520 was designed and certainly drew from it. I looked into what circuit designers may have used as reference in some engineering books from the '60s and '70s. Early transistorized op-amps were first made by George Philbrick and his company [George A. Philbrick Researches, GAP/R]. They were also the first to put them in a 1-inch square modular box, as early as 1962. So, anyway, I learned the 2520 and figured out the different variations over the years. I was even lucky enough to talk to [API co-founder] Saul Walker at an AES show about it one time. That was a fascinating conversation I'll never forget. He's a real engineer. When I built my first 2520-style op-amps, I tried experimenting and took notes with small changes I made. I retested it over and over. Brent really liked the op-amp. That was really important, because he was stressing the circuit in various ways to see if it would fail. He said, "This works really well. We should make it." So, I showed him how I made it; he hired another tech to try and make it for him, but it didn't work for whatever reason. It's just hard to make a discrete op-amp with all those components in a 1-inch square. Brent came back to me and said, "You've already done this; why don't you make it? I'll just buy them from you if you promise to sell it to me for a good price. And why don't you use your first name for your company?" I'm very thankful for his support, and for the company name idea.
You mentioned to me that you went through a lot of experimenting with the epoxy, or whatever the compound is that houses it. Can you tell us about that aspect?
The epoxy that I first used was really hard and it caused problems. When components warm up, they need to move a little bit. The small diodes are made out of glass, and you can't cement them in. That caused some op-amps to go bad early on. I quickly learned that I needed to change something, because you can't fix a potted op-amp once it goes bad. It's a big waste of time and money if you don't get it right in the first place. I started using a softer epoxy. I learned that from John Hardy [Tape Op #15], actually. He uses it in his 990, and he was kind enough to share that info long ago. He was right, and that epoxy is what we use today. It's softer, and it's thermally conductive so the op-amp warms up evenly. You don't have hot spots in there, and it allows the components to flex. It's simple, but it's a big deal.
You want to use epoxy though, right? Because it actually helps it heats up evenly. If it's just the components open to the air, that presents a different set of problems?
It does, but it depends on the op-amp design. You have to thermally couple some of the diodes to the transistors so that when the transistors warm up, it warms up the diodes that are biasing them in a kind-of thermal relationship. In un-potted op-amps, you sometimes see some components glued to each other for this reason.

After the op-amp, what came next? The mic pre, or the EQ?
After the op-amp, Brent wanted to use it in a 312 preamp. So, I redesigned it with some improvements and that became the 312A. I made adjustments to the pad impedance and gain, and I exclusively used Jensen transformers. I remember drawing up the circuit board using Photoshop at that time.
https://tapeop.com/reviews/gear/45/bae-312a-mic-preamp/
Then I decided to experiment because I wanted an equalizer, but I didn't want to copy the 550A. So, I found a topology that I liked and tested some frequencies and the Q [frequency bandwidth] going all the way to 28 kHz. I still have the working prototype. That became the first EQ I made, which was really different than anything else out there. It used similar amps that you'd find in an API 550A, but it used a filter design with characteristics you'd find in an inductor-based design, like a Neve or a Calrec. That was the earlier model E15. I quickly added more frequencies to it and that became the E27 which we still make today.
https://tapeop.com/reviews/gear/121/e27-500-series-eq/
Older Neve modules have an active Baxandall and an active LCR-type equalizer. The Baxandall just makes use of capacitors for tuning the LF and HF, both of which share the same card inside – the B205 (or B180 in older 1066 modules). An LCR circuit is used in the MF with the B211 card (or B181 in 1066 modules). Inside of most electronics textbooks, you'll see mention of . = inductance, = capacitance, and = resistance. If you put the three together, with some feedback around either a discrete or IC-based amplifier, then you can tune to a frequency. The API 550A uses a twin-T filter. It's a way of super-tuning, using resistors, capacitors, and feedback around a discrete op-amp. It can sound very nice and clear. I would think it's great for mastering, as long as you had all the frequencies and boost/cut steps you need. Not as colored as you'd think – but the coloration will come from the other components, such as the op-amp interacting with the output transformer, each with their own limitations. The API 560 graphic EQ uses a type of active gyrator filter, using IC op-amps for each frequency, and another IC for boost/cut. The 2520 in the oldest 560s drives the output transformer, but in the 1980s, API removed the 2520 and even the output transformer (optionally), and put in a couple of push-pull transistors instead. I like it, and it does have a certain sound and characteristic that's different than the 550A. The is somewhat related to this topology, except that I use small Class A amps instead of ICs, and I use the 1122 op-amps for boost/cut, as well as for the output-stage driver through a Jensen output transformer. Plus, there's a Jensen input transformer and another Class A amp, so if the transformer sees the load it likes, and the EQ circuit sees the source impedance it likes, it's a happy unit. This allows more freedom for the filter EQ part of the circuit to add its characteristic sound. The API 554 is a state-variable EQ, using three IC op-amps for each band, with capacitors, to change your tuning. It sweeps around instead of locking into a specific frequency. It's versatile, but it causes more phase shift, and, coupled with the series of IC op-amps, your signal is passing through, [and that] results in that very EQ'd sound. I like it sometimes, and on certain problematic frequencies, it can squeeze into tight spaces in a nice way and solve issues. Many parametric EQs are also the same topology, with some variation – lots of control with the frequency sweeping around, but also lots of phase shift. Another rule to keep in mind: when we see an EQ shelving curve, we don't call it by the frequency point where it peaks, but where it's down −3 dB. So, with a Neve 1073 high-frequency at 12 kHz, that's where it's supposed to be, theoretically speaking, down −3 dB, which means its effect will be greater at higher frequencies. With a bell curve, two −3 dB points are taken at the sides of the peak, and this determines the . If you divide the peak frequency by the bandwidth of the −3 dB points, the result will be the Q number. For example, if you're EQ'ing at 2 kHz peak, and the −3 dB points are at 1000 Hz and 3000 Hz, then bandwidth is 2 kHz. Divide peak frequency by bandwidth, and you get Q = 1. If bandwidth was narrower, you'd have a Q higher than 1; with a wider bandwidth, Q would be smaller than 1. The guys who bought the first E27's were some rappers in L.A. because they liked the big low-end and the higher top-end. It started with Warren G, who came in to buy something else at Brent's shop and saw my EQs there in the 500 Series rack. He was asking me about prices, and I said, "Well, these EQs are $750 each," [which was the introductory price at the time]. He said, "No, just this little thing (pointing to the E27). Not the whole rack." I said, "It's $750." He said, "Just for that? Are you kidding me? Why?" And I had to tell him it had discrete components, as opposed to ICs. and nice transformers. Plus it had expensive custom rotary switches, custom knobs, etc., and it all costs more to manufacture. He ended up buying the whole rack. From there, I got more guys coming in asking for the same thing. That really helped me out early on because there wasn't enough demand for 500 Series, so I'm very grateful for that.
I think I was one of your earlier customers.
Yeah. 12 years?
Over a decade ago! They're just so durable, which I really appreciate.
Servicing a lot of vintage gear over the years taught me a lot about component failure and reliability, and I'm thankful to have worked on so much broken gear early on. It feels good to design equipment that's reliable.
It's probably more work if you have to service it too.
It is. The shipping and servicing end up wasting time that could have been productive for the client, and for us.
So, what came next?
The MA5 preamp, because my friend asked if it was possible to have a Class A amplifier like a Neve Class A, but to put that in a 500 Series format. That was an interesting challenge to make it work on bipolar 16 volts, giving a 32-volt potential instead of the original 24 volts. You have more voltage, so there's more headroom. I remember what Bill Whitlock of Jensen Transformers [Tape Op #104] would say – electrons don't read schematics – so, with that in mind, I designed the circuit the way I thought it would work best. That became the MA5; it was really successful and proved to be ultra-reliable. After that we made the MD7, which is kind of like the op-amp based API 312 / 512 world, but it's got a send and return, stepped gain, and no input pad because I don't like how an input pad can weaken the sound before you get to the input transformer.
https://tapeop.com/reviews/gear/116/md7-500-series-mic-preamp-pedal-interface/
I haven't used these, but I remember we reviewed them.
Yeah, it's what I wanted to do because I don't feel comfortable making clones that I see so much of nowadays. I designed a lot of gear for BAE Audio – like the 10DCF compressor, the 1023, and the 1073MPF – that share similarities to older gear but weren't really clones of anything. I want to keep learning, so I'm always interested in going in a different direction. Now we're making an electronic instrument preamp called the KeyPre. I didn't know about the world of keyboards and synths. I didn't think about it as much until someone came by our booth and suggested it at an AES show in New York. I soon learned that keyboards had different output impedances, different levels, and different ways of interfacing with balanced and unbalanced. So why are most of us using a DI to interface keyboards, synths, and drum machines? It didn't make any sense to me. I studied a bunch of electronic instruments that my friends had; I made the KeyPre so that it interfaced nicely with all of them.
Anything you throw at it keyboard-wise, it's gonna handle it?
It will handle it. Balanced or unbalanced, with any line level and with any sub low-frequency you can throw at it so you get the full bandwidth of your instrument through.
Some synths have super-hot outputs. They're almost line level.
Yeah. Sometimes you don't need extra gain, so you can set the KeyPre at unity or less and get that nice, balanced output.
Will it handle low-level high-impedance things, like a passive Rhodes electric piano?
It should be able to with 32 dB of gain, but for that I'd use the DI input of the MD7 which has a higher input impedance of 10 M (megaohms) since the output of the Rhodes is similar to that of a guitar pickup. We tested unbalanced outputs of the Farfisa and the Juno-60 which had an output impedance 2,000 ohms. That's pretty high, but it works well with the KeyPre. There's a lot more variability in electronic instruments than for microphones. Most microphones are about 150 to 300 with some older ribbons being lower, like 30 to 50 ohms. But with electronic instruments they are all over the place. The KeyPre's input impedance is an optimized 48 kilohms and will happily interface with all of it. You certainly don't want to bottleneck your sound going through a DI. That was the purpose of making the KeyPre. It took me about a year to find the right combination of input and output stages.
So, a DI, especially a passive one, will mess with the impedance and change the frequency response?
A passive DI will put your sound through a transformer, so it depends on the quality of the transformer. There are only a few transformer manufacturers that know how to make a good-sounding DI transformer. But, due to physical and electronic limitations with winding transformers, your input impedance cannot be as high as an active input DI would be. You can get about 150 kilohms, but never as high as 1 megaohm, which is what you need for things like piezo pickups.
Bottlenecking what, exactly?
A lot of times, you're going through a small capacitor placed to protect the input stage of the DI, and capacitors naturally act like high-pass filters, bottlenecking your bandwidth and causing some phase shift. It may be fine for the guitar or bass, but electronic instruments can have a much wider range and need to plug into something that has a frequency response wider than itself so you don't lose anything.
You lose a lot of the bottom-end.
You lose a lot of the details on the very low-end. A lot of keyboards can have notes with very low frequencies.
Tell me a little bit about your most recent venture at Sound City. What are you doing over there, and how did that come about?
Well, I've had a Neve console since 2000, sitting here in this garage for the last 18 years. We didn't have a place for it. After the Sound City movie came out, a friend of mine said, "Don't you have a Neve console sitting in your garage? Why don't you do something with it? Let's make it work." I wanted to work on it at night, so I thought to take it to my house half a mile away from here. I asked my wife if it was okay to have the Neve in our house for a while, and she said it was. She didn't realize it was a 9-foot long console that ended up in the middle of our living room. I had it there for six months, put it all together, and tested all the channels. It was already in great condition, for something made in 1973. Then my friend, Bryan McCurry, turned me on to Blake Mills [Tape Op #115] and Tony Berg [#121]. They wanted to lease Sound City and were looking for a console to put in there. They asked me about leasing my console, and I said, "Sure. Get this thing out of my house, please!" My wife was really happy. [laughs] So, it's there now, and I'm happy to see it being used every day. It's rare for a 45-year old Neve console to have everything working; but, with regular maintenance, it seems like everything is working and it sounds really good. All these years I had the console, I really hadn't heard it until it was in Sound City. The old custom JBL far-field monitors they had in storage were found and put back in, and they sound amazing.
How often do you have to go in and do maintenance? Do you deal with anything else besides the Neve console, or does your responsibility end at that console?
I've got a lot of outboard gear there as well, so it's those things and the Neve console. That's really it. Maintaining it. Cleaning switches, cleaning contacts.
You don't have to worry about any gear that's not yours?
Right, I only maintain the gear that's mine, which is a lot of vintage and some new outboard gear. I'd rather see it be used than to sit here. Plus, I have access to it if I need it. Blake and Tony have a lot of great instruments and amps, and they have their own very qualified techs for all that.
I guess what I'm asking is: is this an active relationship, or is it just like, "Send me my check at the end of the month!"
No, I'm there as needed, and I can use the space myself as needed to test things out. If we need to take something there to test and evaluate it, we can. It's really nice that they're very supportive of new things that come out of here.
So, you enjoy the relationship?
Yeah, they've been great and I'm happy working with them. I was just there listening to one of Blake's tracks they'd recently done, and it sounded unbelievable.
Both those guys are super-talented, super nice people.
Yes, they are. Tony's got Studio B with his vintage API console in there. It always makes me happy every time I go to Sound City. I love seeing the progress of the studio, as well as seeing the dedication and hard work of the entire staff.
What's next for you?
We have a box called the TransDrive, which can house a variety of different audio transformers so you can put your audio through it to get that nice transformer fingerprint on your tracks.
I remember seeing that at NAMM.
I love comng into work, building prototypes, and working on new things. There's got to be a compressor in the future for us. I see more rackmount gear beyond the 500 Series gear in our future.
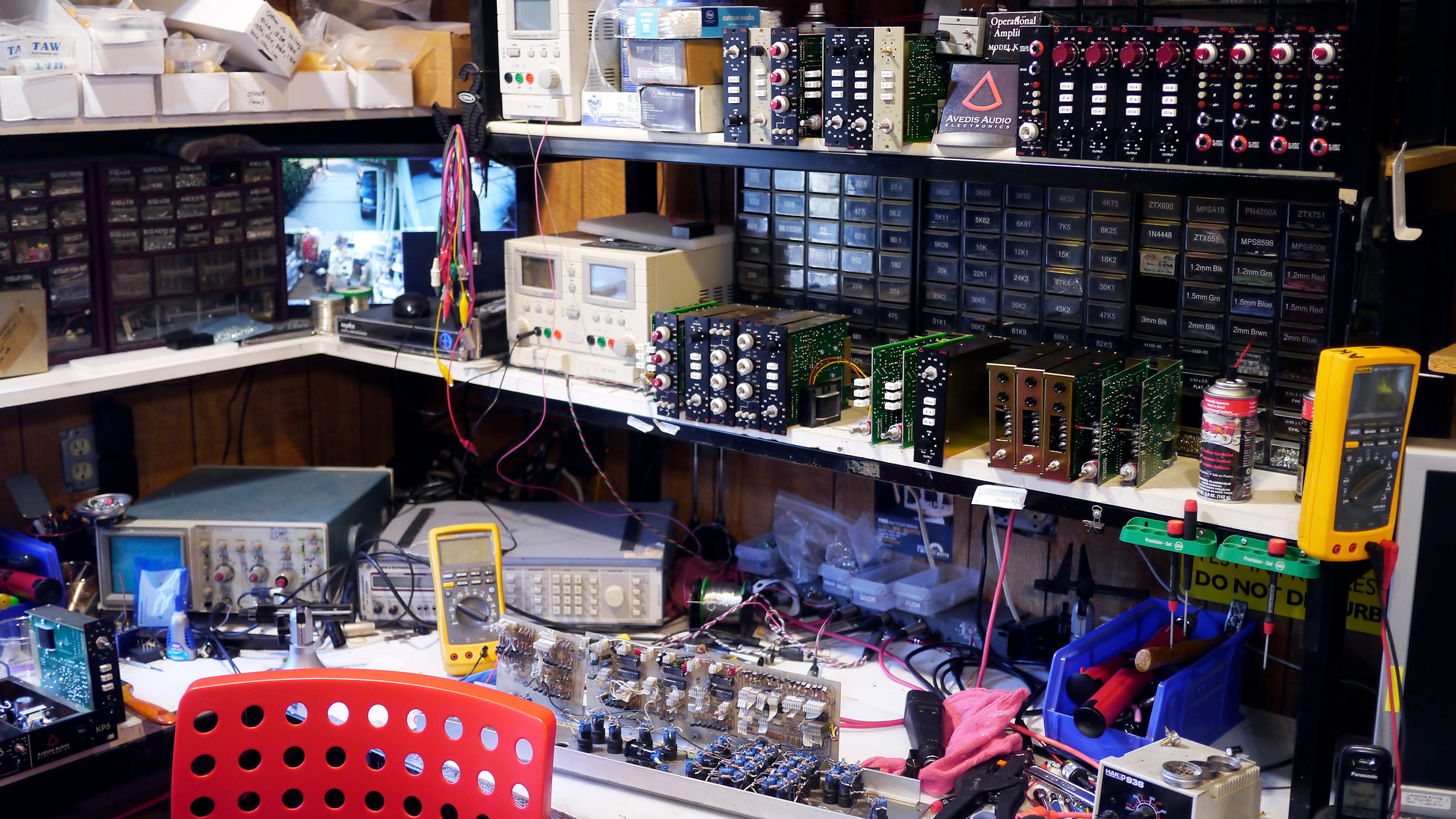
How do you balance the, "I love to make new things" side with the, "Damn, I've got to run a business and keep things moving out the door" side?
That's been the biggest challenge in my life. And, also, how do you balance it with family time as well? That's been really tricky. It's just been whatever's the priority that week, that's what we have to do. But, I'd say coming into work, what I really enjoy doing is building new gear. I love to come in and work on prototyping things, getting stuck on the prototype, being able to think about it overnight, coming back to work the next morning, figuring it out, and getting stuck on the next problem. Problem-solving is what I really enjoy. I don't find as much enjoyment from doing service and repair work, which I never really did, except for friends and close clients, but it's not that fun for me. I'm not learning anything new.
What about distribution and marketing? Who else works here, besides you, Jeff [Watson], and your dad?
My wife helps with accounting, and I have some friends who come in and help me out as needed.
So, the full-timers are you, Jeff, and your dad?
Yeah.
Does Jeff handle more of the business stuff?
He does. He takes care of a lot of the orders, and I take care of the technical side of things. Jeff definitely takes care of all of the business side of things.
It's good to have someone like that.
Yeah, we both wear many hats here and we don't have a marketing department. Sometimes we put pictures up on Instagram and Facebook of new and old vintage gear, which is more educational than it is marketing. We put a lot of effort into the design of our gear while trying out new things, then we figure out in the end what we're going to sell it for. Whereas, I think some larger companies start with a budget and have to design backwards from that amount. Nowadays, you don't even have to be an audio designer because companies in Asia have already done it for you, with pro-audio products ready to ship. All you need to do is design your company logo and place a large order. It's not that one's right and the other is wrong, because everyone is trying to find their place in the audio market.
Is everything more or less made in southern California? I assume you're not making circuit boards here?
Yes, everything is made here, and our circuit boards are manufactured in Northern California. All the boards get populated by my dad. My retired dad was a welder, back in the day, who'd worked in off-shore oil platforms and the metal industry in Detroit. We joke now and say he's still doing welding, but miniature welding with a soldering iron. But just not as dangerous, or bad for your eyes.
He enjoys it?
Yes, he does. He's retired, and he wants something to do. He's like me, a workaholic. It's a great help, and it works out for us. If we find out that something's not right, we can immediately get it fixed and move on from it. Part of the reason why the gear is reliable is because of the attention to detail. Being a smaller company, we can really see what's going on at every step of the way, with every component. My dad's been really helpful with it. Otherwise I'd have to outsource it and get an assembly company to do it. And I'd probably have to deal with a greater chance of errors, especially if they put our boards through a wave soldering machine with the temperature too high, cooking the components and shortening their life. The way that he solders it, the components don't get heat-stressed. Everything gets done here. We're a productive little shop.