Louder Than Liftoff is a relatively young pro audio company. They caught my eye with a unique take on both the 500 series EQ and the two bus processor. A small, two-man operation, born of a passion for impeccable sound, the company takes founder Brad McGowan’s DIY aesthetic and his NASA-level engineering chops, and combines them with extremely interesting and, in my experience, excellent results.
Your professional engineering background is in aerospace. How did you get on the path to designing professional audio gear?
I started playing guitar when I was 18 and quickly got into recording. I had a cassette, a 4-track. I think I had always been curious about electronics. I had one of those RadioShack kits with the little springy things that I would make different circuits with when I was a little kid. When I got my first tube guitar amps I never understood why I had to pay some guy to do this magical thing to my amp to make it sound good. So I started to learn about guitar amps and basic electronics, and I got comfortable enough sticking my fingers into the amplifier to learn how to work on them. That turned into modding tube amps, and later building them.
Pro audio was an obvious point of departure?
I met a guy that was really big into the whole DIY scene, like the GroupDIY forum [www.groupdiy.com]. We had a total bromance centered around electronics, and we’d get together and build projects, like 1176 and a SSL G [style compressors]. I was also modifying a lot of gear. Then one day I was just like, “I want to design something of my own, from scratch.”
Did you study electrical engineering in school at all?
I had taken some electronics courses in college, but the course itself was very mathematically based. It wasn’t practical, like, “How do you actually make a circuit?” It was like, “This is how an op amp works. Do these equations.” When I was in the process of moving, I was going through old books, found some of my textbooks, and thought, “Oh, here’s my electronics textbook. Should I save this? Nah.”
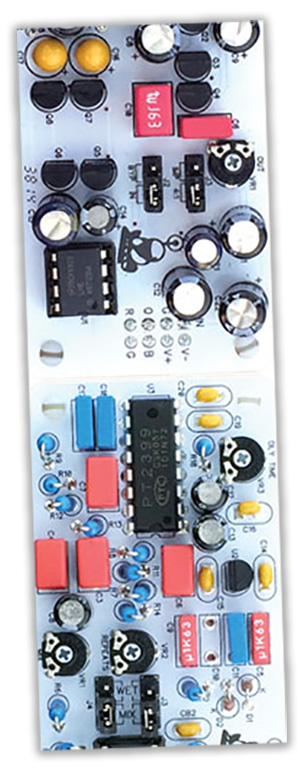
So what was your practical learning process?
I just started reading a bunch online and staring at schematics. My degree is in aerospace engineering; I work as a mechanical engineer, as a designer. It’s like I have this very strong design background, and a very systems-level approach to design. It was like learning a new foreign language, or a different dialect.
What was your first design?
I started designing an outboard API-style >mic preamp. I didn’t know how to go through the manufacturing process to make a piece of pro audio gear. That was right around the time that I met Greg [Scott] from Kush Audio. I was telling him about all my DIY projects, and we clicked creatively. He said, “We should work on something together.” Somehow I managed to convince him that I knew what I was doing, even though I had no credibility as a circuit designer. We brainstormed a bunch of different products, and we ultimately settled on doing his monitor controller, which became the Gain Train.
And the Kush Electra EQ was next?
Greg had this circuit from an old console from the ‘70s, and he said, “You need to hear this EQ. It’s really cool. It sounds like a >wah-wah pedal when you sweep it.” At first it was gonna be this big, elaborate tube EQ. Then somewhere along the way, it was like, “Let’s make it for the 500 series.” When we made the first prototype, we thought, “Something is missing...” That’s when I came up with the idea of adding in the Baxandall low-frequency shelf, with boost and cut. There is a jumper, or a switch, on the PC board that allows you to either have a fader or the low-frequency shelf. We made a couple of tweaks to the frequencies on the high-pass filter and it all came together from there. We gave it a slight bit of resonance. That EQ has done really well.
Did that give you the impetus to start your own company, Louder Than Liftoff?
Yeah. I designed [what became] the Chop Shop EQ, and was shopping it around to people. I asked Kush if they wanted to put it out, but he was focusing on other projects, so he passed. I was talking to Peter >Montessi from A-Designs, and it was maybe going to be a Pete’s Place product. He passed it around to all his guys, but they didn’t really get it. They didn’t really see who would use it. I was trying to explain, “When I’m tracking, and I’m working really quickly, it’s easier to just turn the knob.” They said, “But why wouldn’t you just move the >mic?” And I replied, “Well, I don’t want to move the >mic. I just want to turn the knob.”
I think it’s different for those of us who’ve never really had an assistant engineer.
There’s this total difference in perspective of how to get sounds, I guess. Peter said, “You should put it out.” That was the birth of the company.
What was the genesis of your latest product, the Silver Bullet?
Bill Pearson (“drBill” as he’s known online) and I had become friends through Gearslutz.com. We were both on these similar journeys, so we combined all our thoughts and developed the Silver Bullet to put the API and Neve flavors together. He said, “You’ve got to have the ability to go API into >Neve, or Neve into API.” Which we did. You can use just one, or the other as well, if you like. Initially, [the prototype] was just a circuit board that Bill mounted to a piece of plywood, and it sat on his console with wires hanging off of it. People would come to the studio and ask, “What is that?” He’d say, “That’s the Silver Bullet.” It took us about three years to develop it.
And it’s got EQ as well?
Right. Mojo amps, as we call them, plus tone shaping – high and low-pass filters that flank a two-band Baxandall EQ. The high-pass filter has a slight resonant bump, at about 40 hertz – I tried to make it sound like the bottom end of my Studer. It basically just tightens things up, but still keeps them big. You engage the Mojo amps by pressing the Mojo button, and then there’s a selector which chooses the API stage or the Neve stage. It can go API cascading into Neve, or the other way with Neve into API. It’s just simple input and output. You can use it to subtly shave transients; you can take a whole drum sub-mix and get extra volume, or put it on your mix bus. There is this nice enhancement thing it does that makes the whole mix open up, especially the >Neve circuit. It does this bloom in the low midrange. It gets really fat, especially as you push it. It’s really velvety in the midrange and top-end.
And then you can toggle to Mic mode for tracking?
In the design process I eventually realized, “I don’t think it’d be too hard to add a mic preamp to this thing so I can actually record through it.” It would be an all-in-one solution. Just switch to tracking mode, and now you’re overdubbing through the same processing. We have Mic and Mic+. Mic+ is more input gain for quieter signals, like ribbon microphones. I worked hard on the mic pre section to make it pair up well with ribbon mics and dynamic mics. It definitely helps inject some life into microphones like that.
Did you work hard to keep unity gain, so users don’t fool themselves by making things louder?
Yes; any complementary pair of settings roughly gives you unity gain.
Is it transformer balanced?
There are transformers that are part of the processing. The inputs and outputs are all electronically balanced. I present a certain interface, and then I do stuff behind the curtain. I don’t want to give everybody control of every parameter. It seems like a simple box when you look at the front panel – it only has eight knobs – but there’s a lot going on behind the scenes. There are 15 relays in the box, so every time you switch something there’s a ton of signal getting re-routed.
There is a lot of dialogue around wanting to understand equipment, but the average person has almost zero tech chops.
Especially more so these days. Because it’s becoming so easy to get into recording, and you can buy great gear for not a lot of money. We have more artists recording themselves. And so I feel like the interface needs to be artist-friendly, and not technician or engineer-friendly.
So what’s next?
Top secret products! I’d love to do more Colour modules.
You designed four modules for the DIYRE Colour 500-series (small, affordable, and swappable tone circuits)?
Right. That format is becoming quite popular and is kind of exploding. Black Market Modular debuted the Eurorack version of Colour, which expanded the market. Peterson, from DIY Recording Equipment, and myself collaborated with William Matheson from WMD, who designed the Black Market Modular Eurorack Color Palette, and we made sure that everything was going to be cross-compatible. [We ensured] the 500 series >Colours would work in the Eurorack Color Palette, and vice versa.
What are you saying about recording with your products? It feels like you have a point of view.
I think I definitely do. It’s fun to geek out over the technical aspects of recording, but at the end of the day you’re trying to make music, which is not a technical thing. It’s an emotive, artistic pursuit. Because we have more artists becoming part of this craft than guys in lab coats, the products need to cater to their level of expertise and how they expect to interface. The gear should be more of a musical instrument than a piece of lab equipment. I’ve had people say, “You need to have more markings. I want to know what the frequencies are. What the heck does Bass or Presence mean?” From a technical point of view, I could tell you. I could make some plots and you could see what those frequencies are. But if you’re trying to make music and you want more bass, you should be able to turn around and hit the bass button.